Metal Stamping: Innovations Driving Market Development
Metal Stamping: Innovations Driving Market Development
Blog Article
Releasing the Possible of Metal Stamping: Professional Tips and Finest Practices Revealed
In the realm of steel marking, where precision and effectiveness power supreme, the quest to maximize processes and unlock covert capacities is a continuous pursuit. As we browse through the elaborate world of metal marking, a better look at the intricacies of tooling layout, product selection, production effectiveness, top quality control, and arising trends guarantees a prize trove of insights waiting to be discovered.
Tooling Layout Optimization
Maximizing tooling design is vital for boosting performance and accuracy in steel stamping procedures. A well-thought-out tooling design can significantly affect the top quality and cost-effectiveness of steel marking procedures. By carefully taking into consideration aspects such as material choice, die setup, and component geometry, makers can simplify manufacturing procedures and enhance total product top quality.
One trick facet of tooling style optimization is selecting the most ideal materials for the punches and passes away used in the marking process. Proper die layout can assist prevent concerns such as wrinkling, tearing, and extreme springback, leading to higher manufacturing yields and lowered scrap rates.
Furthermore, enhancing component geometry through tooling layout can help decrease product waste and production time. By meticulously shaping passes away and punches to match the wanted part requirements, makers can achieve tighter resistances and improved part top quality. Generally, investing time and resources in maximizing tooling style can lead to considerable long-lasting advantages for metal marking procedures.
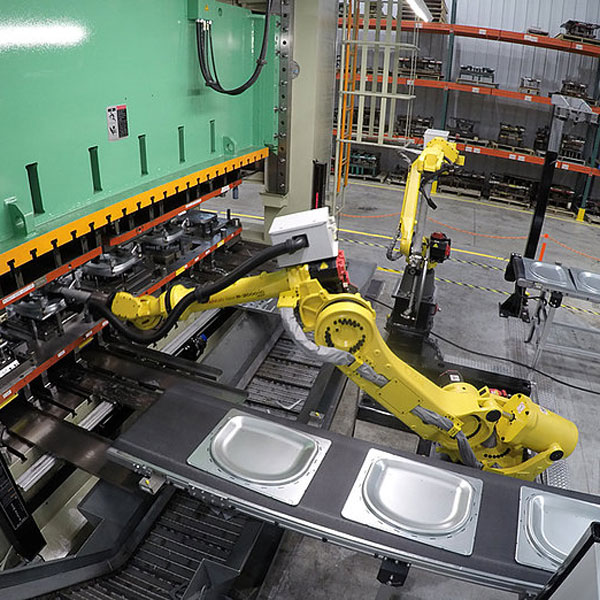
Material Option Methods
Purposefully choosing products for metal stamping tooling is extremely important for ensuring longevity and efficiency in manufacturing procedures. When selecting products for metal marking applications, numerous key factors must be considered. The first consideration is the kind of material being stamped. Different materials, such as light weight aluminum, stainless-steel, or copper, need certain tooling materials to guarantee ideal performance and long life.
An additional important element in material option is the predicted manufacturing volume - Metal Stamping. For high-volume manufacturing runs, tooling products with superior wear resistance and sturdiness, such as device steels or carbide, are frequently preferred to stand up to the rigors of continual marking operations
Furthermore, the intricacy of the stamping layout and the required accuracy also play a substantial function in product choice. For intricate stamping patterns or tight resistances, materials with high thermal conductivity and superb machinability, like beryllium copper or tool steel alloys, might be better to achieve the wanted results.
Manufacturing Effectiveness Strategies
To improve making output and reduce manufacturing prices, executing effective strategies in metal stamping procedures is vital. One crucial strategy for improving manufacturing efficiency is investing in automation. Automated metal marking machines can perform jobs with accuracy, uniformity, and at a much faster rate than manual labor, causing raised productivity and reduced cycle times. Additionally, executing predictive maintenance practices can aid prevent unforeseen downtime by recognizing prospective devices failings before they take place. By consistently keeping track of equipment efficiency and resolving concerns proactively, makers can maximize production timetables and minimize disruptions.
One more technique to boost production effectiveness is through continuous procedure enhancement. Conducting normal audits and performance assessments can aid determine bottlenecks, inadequacies, and locations for enhancement within the steel stamping process. By assessing data and feedback from these analyses, producers can implement targeted remedies to improve procedures, boost throughput, and maximize total effectiveness.
Furthermore, taking on lean manufacturing concepts, such as 5S method and Kanban systems, can help get rid this post of waste, improve process, and enhance general performance in metal marking operations. By cultivating a culture of constant improvement and equipping staff members to contribute concepts for efficiency gains, makers can unlock the full possibility of their metal stamping procedures.
Quality Control Procedures
Building on the foundation of efficient production methods in steel marking procedures, making sure rigid quality assurance actions is vital for keeping product criteria and customer contentment. Quality control in steel stamping entails systematic examination, screening, and monitoring of the production processes to determine and remedy any type of deviations or flaws that could jeopardize the last product's stability (Metal Stamping). Carrying out steps such as regular tools upkeep, in-process examinations, and detailed screening of finished parts can assist spot issues early on and prevent pricey rework or product recalls
In addition to proactive high quality control steps, it is necessary to establish clear high quality criteria and requirements that straighten with consumer demands. Routine audits and evaluations of quality processes can aid recognize locations for enhancement and guarantee uniformity in item high quality. By promoting a culture of top quality awareness among employees and providing ample training on top quality control treatments, producers can enhance general item dependability and brand credibility. Ultimately, buying robust quality control gauges not only safeguards versus issues and non-conformities but likewise leads the way for sustained business development and customer commitment.
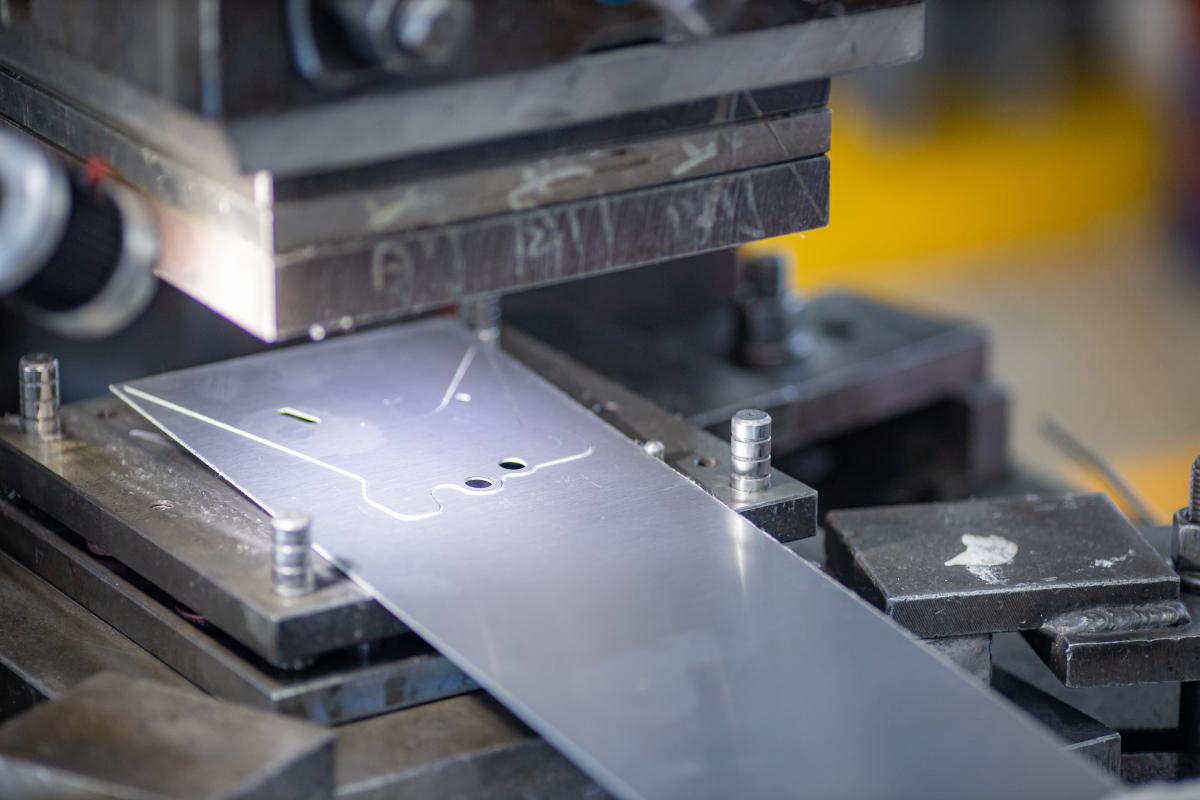
Innovative Metal Stamping Technologies
Improvements in steel marking innovations have actually changed the click here for more info manufacturing market, improving performance and accuracy in the manufacturing procedure. Among the most considerable advancements is the advancement of servo press modern technology. Servo presses use unparalleled control over the marking procedure, permitting for changes in speed, dwell, and force time with remarkable accuracy. This level of control causes greater high quality parts, decreased downtime for tooling changes, and increased total performance.
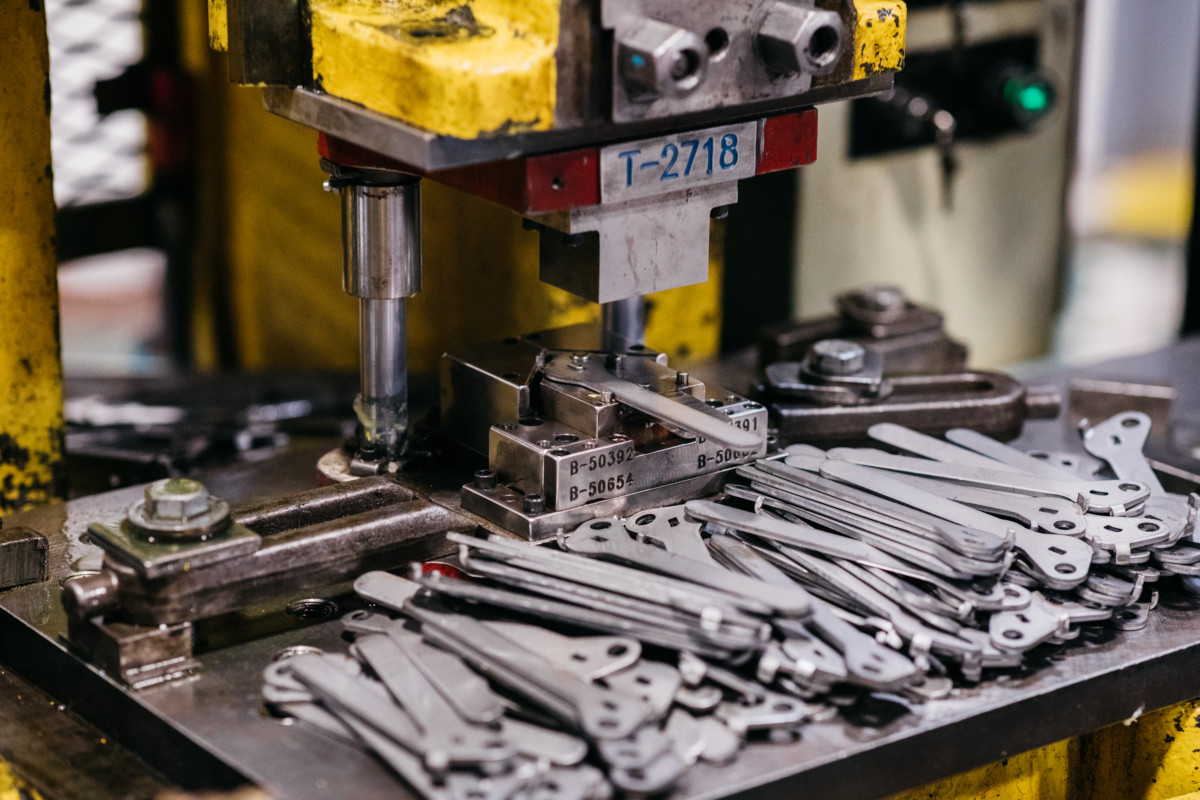
Furthermore, the adoption of additive production methods in metal marking, such as 3D printing of die components, has look at these guys structured the tooling layout and production process. This method permits better design flexibility, rapid prototyping, and cost savings in tooling production. By leveraging these innovative technologies, producers can unlock new levels of efficiency, quality, and competitiveness in the metal marking market.
Final Thought
Finally, the optimization of tooling layout, strategic material choice, efficient production methods, top quality control actions, and cutting-edge innovations are necessary for unleashing the full capacity of metal marking. By applying these ideal practices and experienced suggestions, suppliers can improve performance, raise high quality, and stay competitive in the steel stamping sector. It is essential for firms to continually review and enhance their procedures to accomplish success in this area.
As we browse through the intricate globe of metal marking, a better look at the intricacies of tooling layout, material selection, manufacturing efficiency, top quality control, and emerging trends assures a treasure chest of insights waiting to be uncovered. A well-thought-out tooling layout can dramatically impact the top quality and cost-effectiveness of metal stamping operations.Structure on the foundation of reliable production strategies in metal marking processes, making certain strict top quality control steps is necessary for maintaining item requirements and consumer contentment. Quality control in metal stamping entails systematic assessment, screening, and tracking of the production refines to identify and remedy any variances or issues that could jeopardize the last product's stability.In verdict, the optimization of tooling design, tactical product option, efficient production methods, top quality control measures, and innovative innovations are crucial for unleashing the full capacity of metal marking.
Report this page